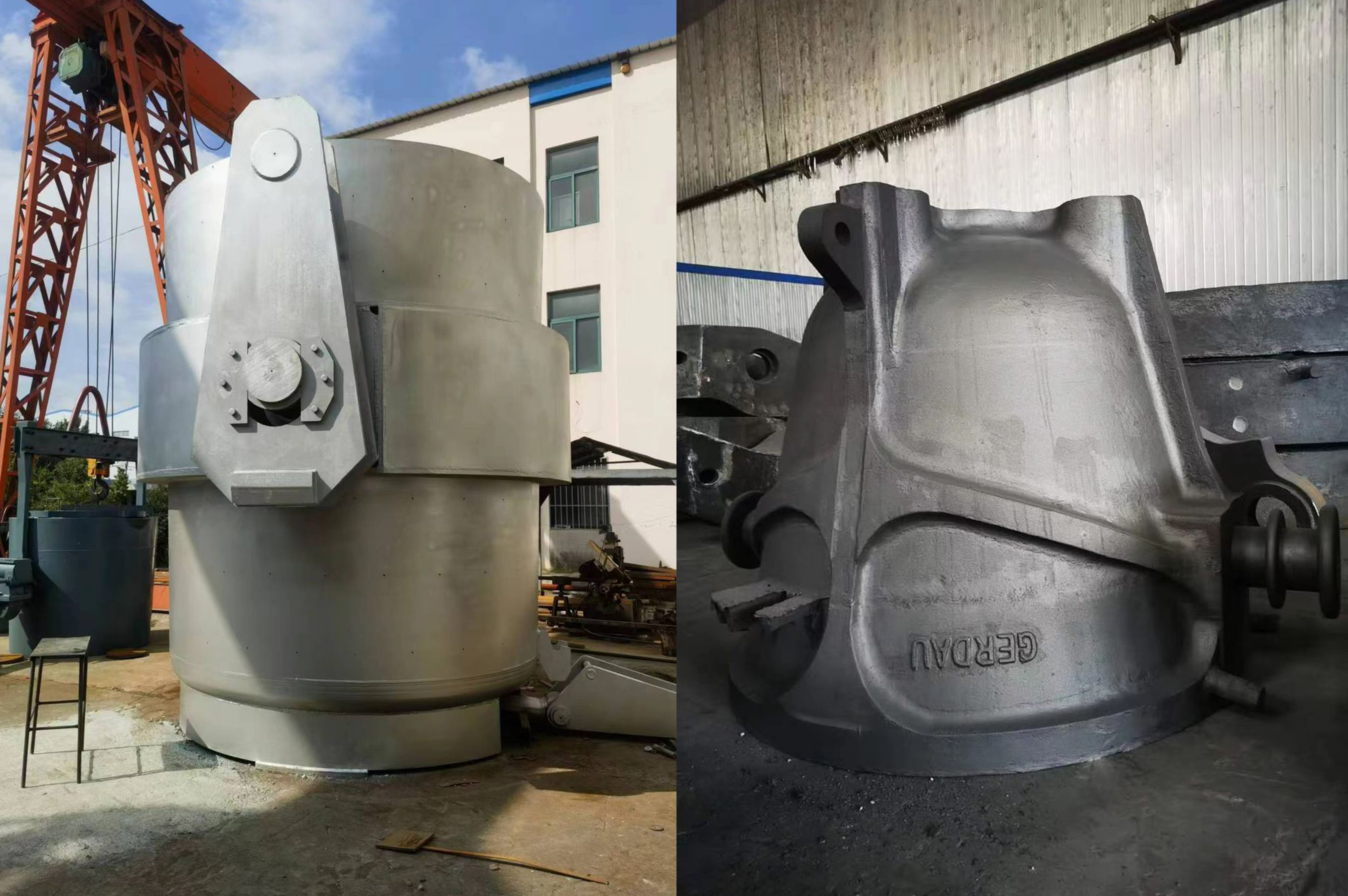
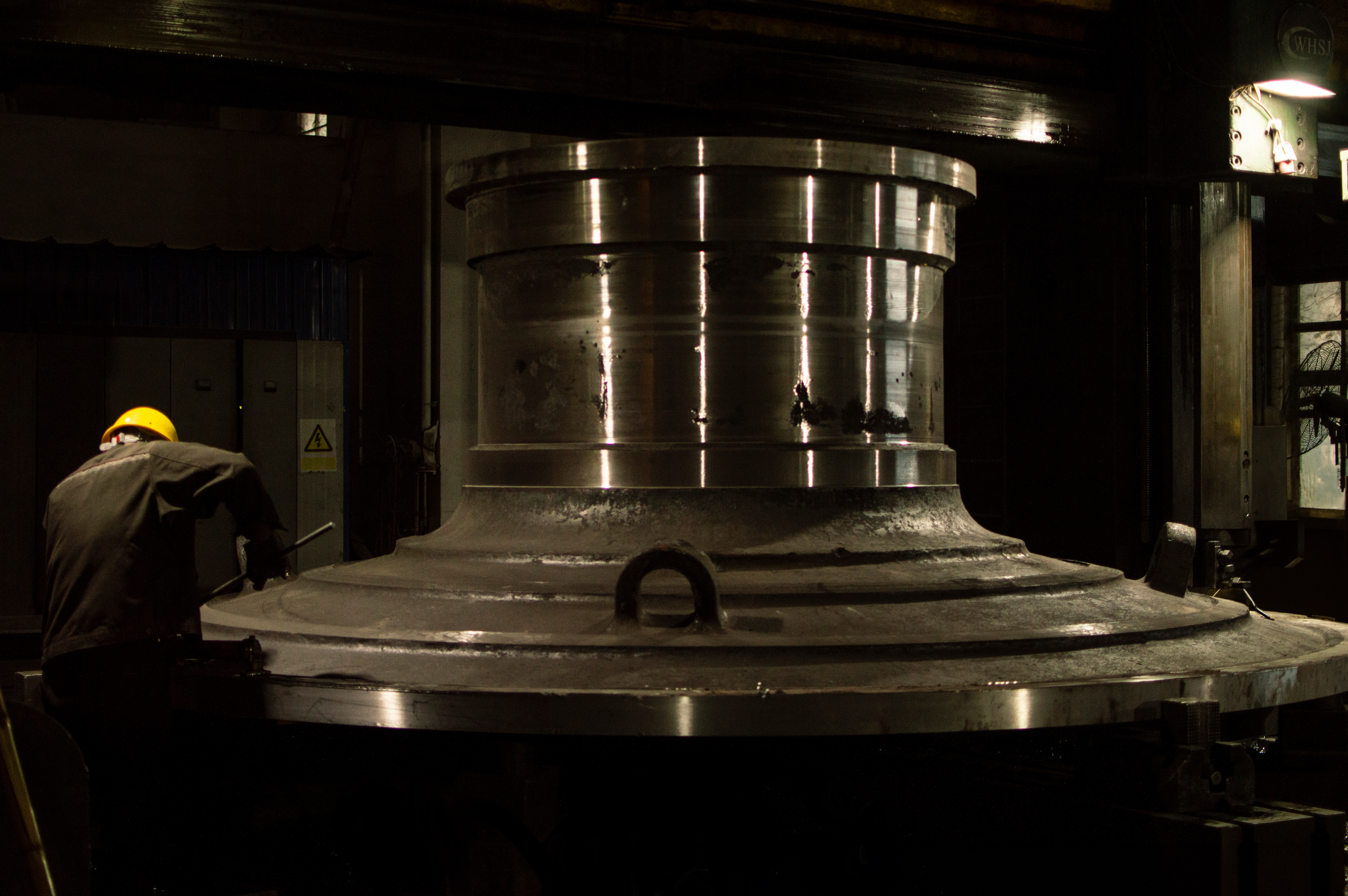
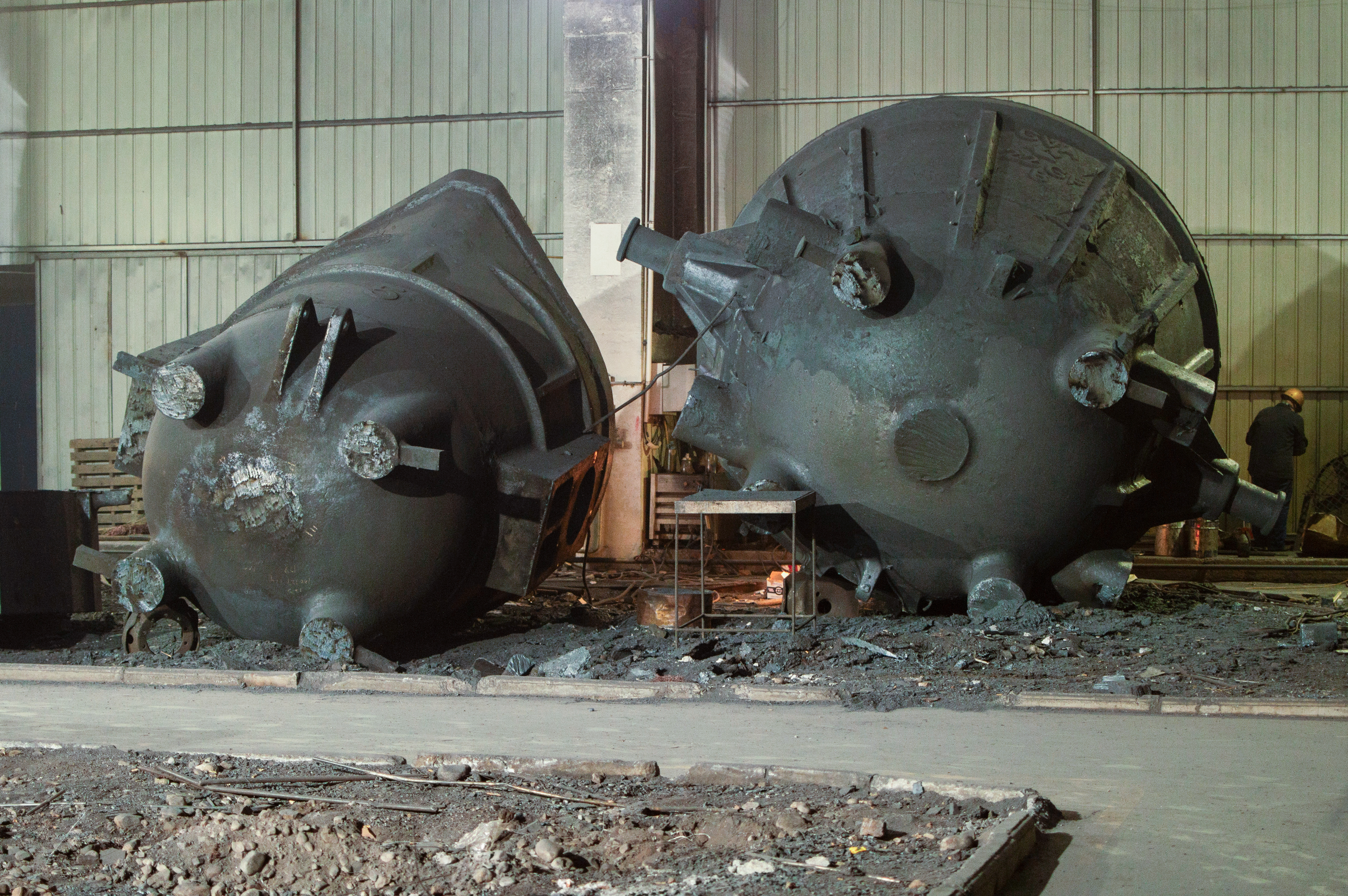
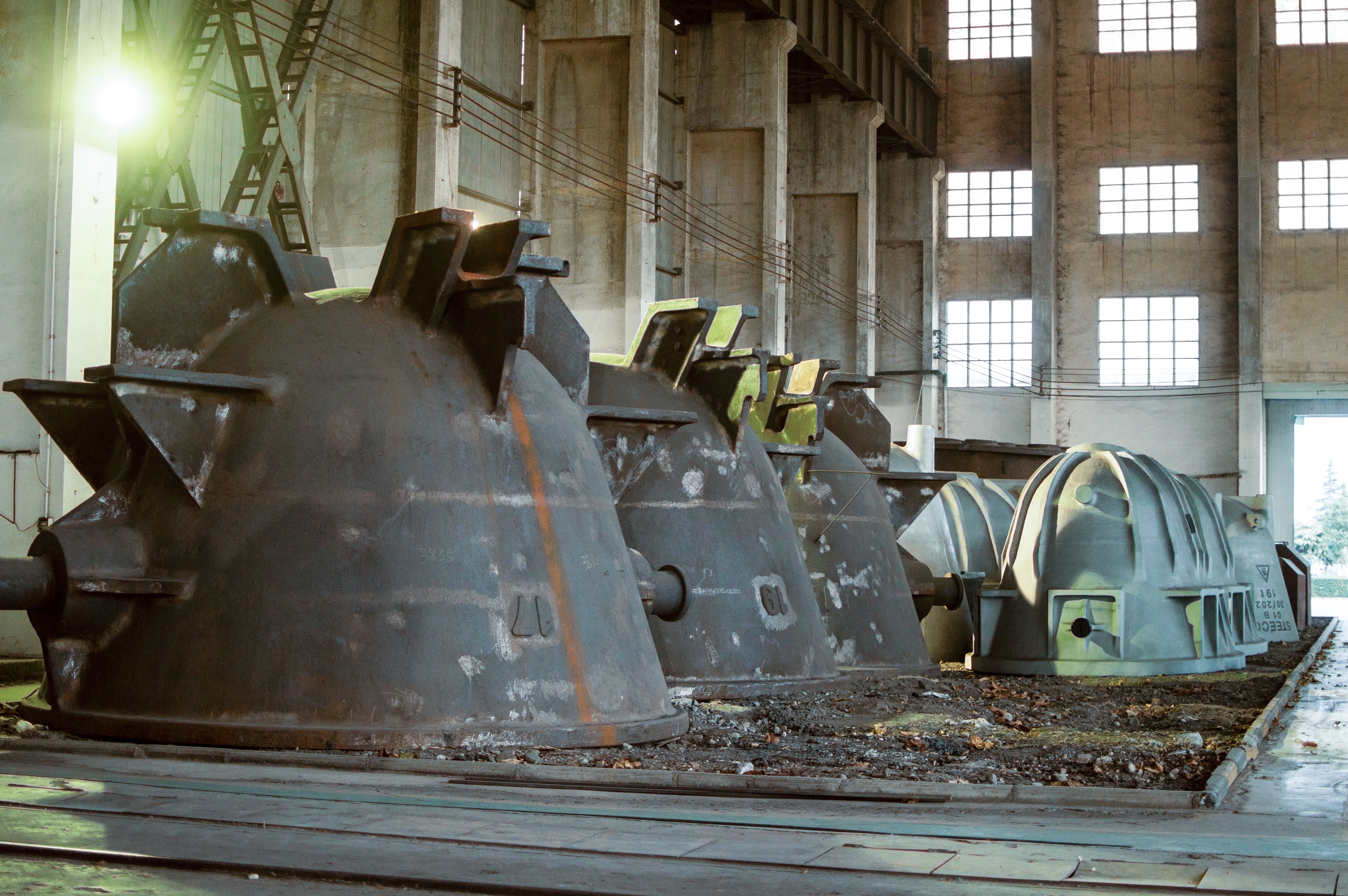
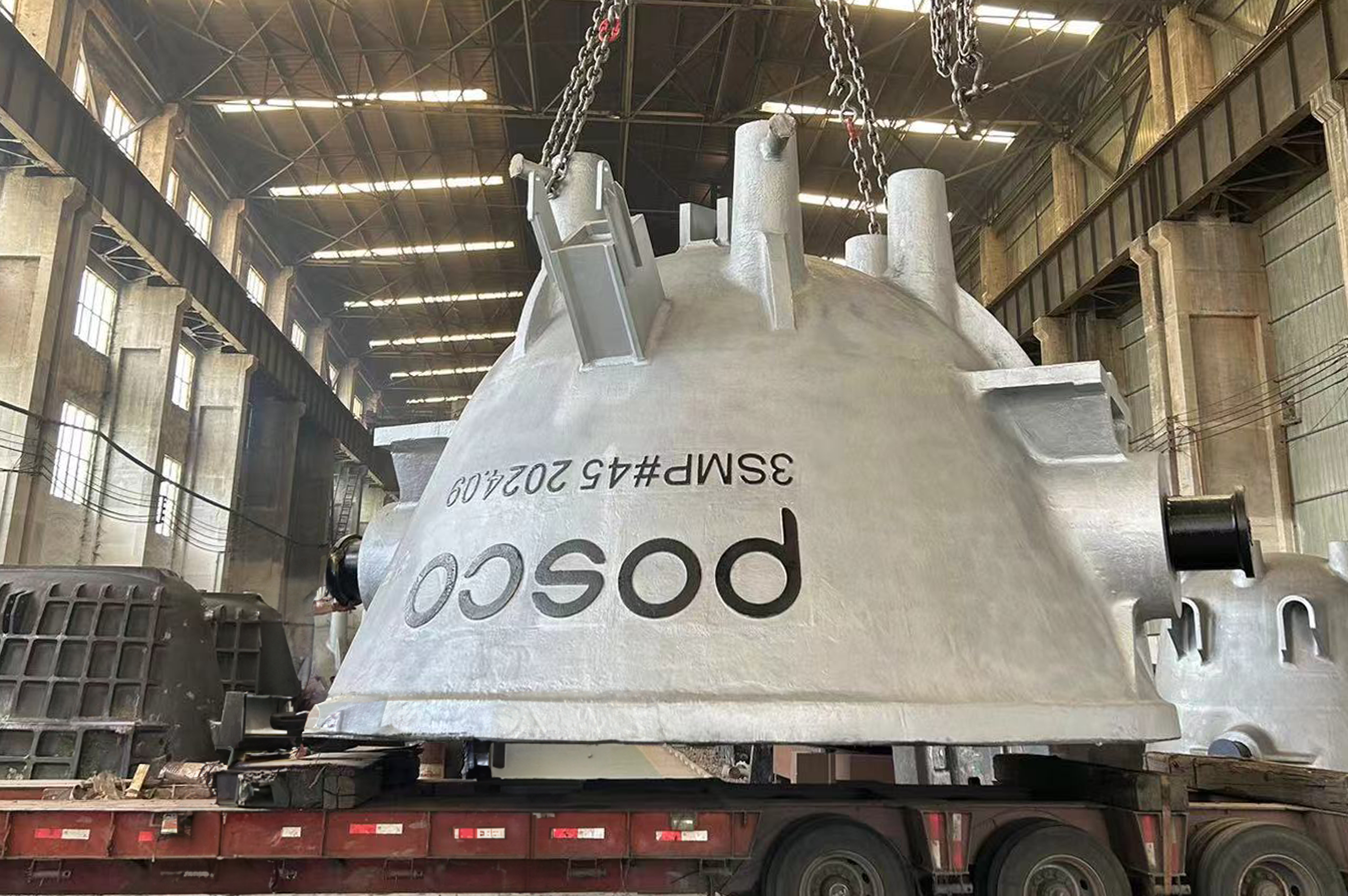
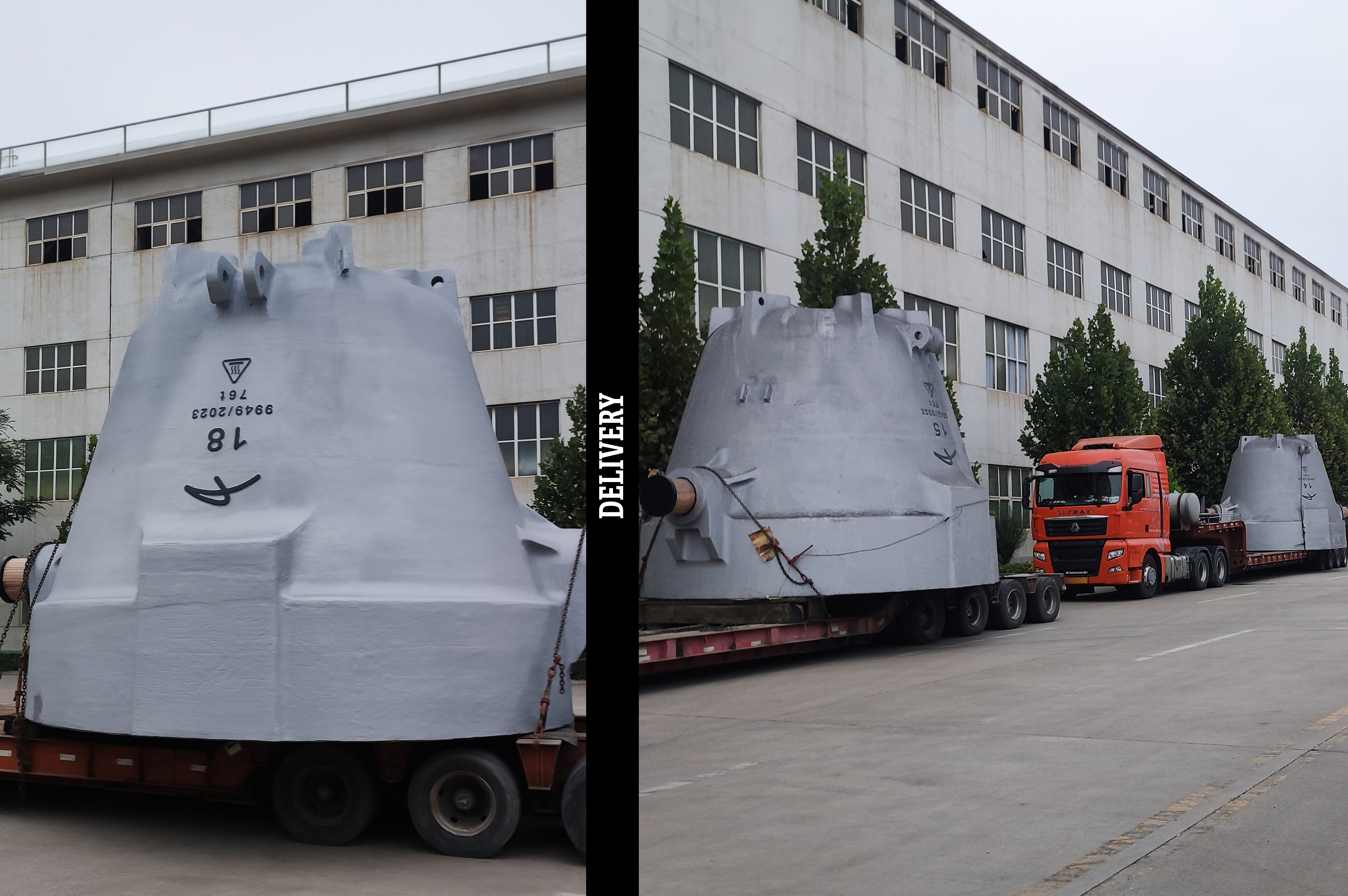
Our slag pots are offered in a weight range from 1 to 85 tons, providing flexibility for diverse applications.
We can cast pots in a wide array of shapes and styles, accommodating various mounting systems and transportation methods. Each slag pot undergoes meticulous design and engineering to meet precise custom specifications. Furthermore, we employ meticulous testing methodologies, including magnetic particle testing and ultrasonic testing, to guarantee the integrity and performance of our products.
Our advanced manufacturing capabilities incorporate modern technology, allowing us to produce pots with robust trunnions using both "cast in forged" and "interference fit forged" methods, the latter achieved through a cryogenic process. This ensures the highest level of trunnion strength for secure and reliable operation.
Our products adhere to rigorous quality control measures, encompassing final chemistry and mechanical properties. Each slag pot undergoes meticulous design and engineering to meet precise custom specifications.
At Machina Masters, we specialize in creating custom-designed solutions that meet the unique needs of our clients. Our team of experienced engineers collaborates closely with you to understand your specific operational requirements, from capacity and dimensions to material performance under extreme conditions. Using advanced CAD software and precision simulation tools, we design slag pots and industrial components that deliver optimal functionality, durability, and efficiency.
Every slag pot and industrial component undergoes rigorous quality control processes to ensure it meets the highest standards of safety, durability, and performance. From dimensional checks and material analysis to advanced non-destructive testing methods like ultrasonic and radiographic inspections, we leave no detail unchecked. Our commitment to quality extends beyond the manufacturing process, with every product thoroughly inspected and tested to ensure it performs flawlessly under the most demanding conditions.